Cooling a CPU, or a GPU.
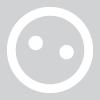
The funny thing about cooling a CPU too much, is the metals get less conductive unless you run more wattage though the CPU to excite the conductor metals and make them more conductive because they are at ideal temp. Heat them too much, the conductive metal traces melt, heat them too little, they do not conduct well and you get slower electron flow-- to a degree. So, each CPU has an ideal temp operating range because of the metals and the ability of the non-conductive insulating materials to not conduct, and those materails have good operating temp ranges also.
Thrax's article on putting a computer in a very efficient cooler shows something interesting-- you can oc more that way because the cooling is so effective that the insulation materials are kept cold, and even the lowest temp melting materials do not melt while the conductive materials are run at ideal inner conductive trace temps for ideal conductivity. The bath was so effective that the computer could be OC'd more-- I do not know if he tried to see how much he could OC the computer, but the bath effect plus a cooling of bath material woudl have given the best results possibly for pure OCing.
Water cooling has limits mostly due to dew point of surroundign material and propagation of water molecules through the tubing causing condensation, but the biggest casue fo condensation in a water cooling system is contact of humid or damp air against cold things causing a localized dew point effect-- water droplets appear to cather on tube, but most moisture is coming from surrounding damp air, not the coolant flowing in the block.
So, how do you get past this???
Here's an idea--- take your blocks, insulate them except for your contact surface.
Encapsulate the metal cooling core in nylon, tyvek, or for a lower temp difference cooling, even liquid electrical tape, EXCEPT for the contact surface, and insulate all the INCOMING tubes to each block also. For REAL extreme cooling, you get to insulate ALL of the tubes. Now you have air against surfaces that are not cold, much less condensation, but the contact surface is cold. Ceramique will not conduct much water at all.
To control, you need a circuit that senses external CPU temp, and maintains it in a range by controlling the coolant temp so things neither get too cold in CPU nor too hot. A 12 V control circuit can be used, to flip a switch for a compressor. AC control cirucits use about 24 volts, a closed 24 volt circuit could also be used, but the temp sensors for computers that are commonly available use 12 V or lower typically as you get good thermal to voltage level responses, or inverse resistance effects, in the 7-14 V range. (Thermistors used for fans respond in this voltage flow range, inversely, and most thermal sense devices can work in this range also).
I'll give you a couple ideas-- My Prescott best likes a 60 C internal temp, for whatever reason. At 68 C it is about 90-93% efficient. So, we need to keep CPU CORE in the 58-62 C range ideally. You can do two things to cool-- secondary cooling, or primary cooling. Secondary cooling always is inefficient versus primary (direct contact) cooling. Thrax's bath proved that. Period. Excellent point made, well done experiment.
So, how do we get more primary cooling?? By doing pinpoint, direct contact applied cooling at the things that heat up, guaged to the cooling demand of those things. so, temp reactive cooling is needed, and if you want to cool everything, you need pinpoint zonal cooling. More flow of cold against hot cools more, lower temp flow cools more. So, what if we were to use zoned flow control and overall temp control of a cooling system, insulate piping to keep the surronding atmosphere from warming the coolant in the pipe, and also to prevent condensation as much as possible???
The combo of the three is what we want. Flow control (more pinpoint than the computer coolant systems now have, using temp change feedback and flow control), coolant temp control, using temp feedback circuits to control cooling and zone flows to demand based on temp rise control, PLUS direct pinpoint uninsulated contact points with insulation of all the rest except the compressor or vacuum pump (which needs to be Externally EXOTHERMIC and needs to have drainage and evaporation below it) as you will get some condensation around it ought to let us get a more effective cooling system.
Make sense??? If yes, let's discuss howto. With a cold fluid flow cooling system in mind.
Thrax's article on putting a computer in a very efficient cooler shows something interesting-- you can oc more that way because the cooling is so effective that the insulation materials are kept cold, and even the lowest temp melting materials do not melt while the conductive materials are run at ideal inner conductive trace temps for ideal conductivity. The bath was so effective that the computer could be OC'd more-- I do not know if he tried to see how much he could OC the computer, but the bath effect plus a cooling of bath material woudl have given the best results possibly for pure OCing.
Water cooling has limits mostly due to dew point of surroundign material and propagation of water molecules through the tubing causing condensation, but the biggest casue fo condensation in a water cooling system is contact of humid or damp air against cold things causing a localized dew point effect-- water droplets appear to cather on tube, but most moisture is coming from surrounding damp air, not the coolant flowing in the block.
So, how do you get past this???
Here's an idea--- take your blocks, insulate them except for your contact surface.
Encapsulate the metal cooling core in nylon, tyvek, or for a lower temp difference cooling, even liquid electrical tape, EXCEPT for the contact surface, and insulate all the INCOMING tubes to each block also. For REAL extreme cooling, you get to insulate ALL of the tubes. Now you have air against surfaces that are not cold, much less condensation, but the contact surface is cold. Ceramique will not conduct much water at all.
To control, you need a circuit that senses external CPU temp, and maintains it in a range by controlling the coolant temp so things neither get too cold in CPU nor too hot. A 12 V control circuit can be used, to flip a switch for a compressor. AC control cirucits use about 24 volts, a closed 24 volt circuit could also be used, but the temp sensors for computers that are commonly available use 12 V or lower typically as you get good thermal to voltage level responses, or inverse resistance effects, in the 7-14 V range. (Thermistors used for fans respond in this voltage flow range, inversely, and most thermal sense devices can work in this range also).
I'll give you a couple ideas-- My Prescott best likes a 60 C internal temp, for whatever reason. At 68 C it is about 90-93% efficient. So, we need to keep CPU CORE in the 58-62 C range ideally. You can do two things to cool-- secondary cooling, or primary cooling. Secondary cooling always is inefficient versus primary (direct contact) cooling. Thrax's bath proved that. Period. Excellent point made, well done experiment.
So, how do we get more primary cooling?? By doing pinpoint, direct contact applied cooling at the things that heat up, guaged to the cooling demand of those things. so, temp reactive cooling is needed, and if you want to cool everything, you need pinpoint zonal cooling. More flow of cold against hot cools more, lower temp flow cools more. So, what if we were to use zoned flow control and overall temp control of a cooling system, insulate piping to keep the surronding atmosphere from warming the coolant in the pipe, and also to prevent condensation as much as possible???
The combo of the three is what we want. Flow control (more pinpoint than the computer coolant systems now have, using temp change feedback and flow control), coolant temp control, using temp feedback circuits to control cooling and zone flows to demand based on temp rise control, PLUS direct pinpoint uninsulated contact points with insulation of all the rest except the compressor or vacuum pump (which needs to be Externally EXOTHERMIC and needs to have drainage and evaporation below it) as you will get some condensation around it ought to let us get a more effective cooling system.
Make sense??? If yes, let's discuss howto. With a cold fluid flow cooling system in mind.
0
Comments
Interesting idea.
The challenges with present watercooling/peltier systems is that they are "on" or "off". The simpler the circuit; the less expensive the entire unit is. Also the size factor.
To have a system that reacts to temperature you would have to have some sort of setup similar to the normal fridge. When the temperature reaches a certain point the pump kicks in and lowers it. The problem is space. You could end up with a second case housing the entire cooling unit.
The system would also be time reactive to a point without peltier assistance. If it were only water cooled then there would be the time elapsed from the first point in time where the sensor on the processor sends a signal asking for more cooling...to the time where the system could "cool" the fluid down and circulate the cooler fluid to the processor. This would obviously be longer than a minute.
A peltier device with on/off control may provide the more immediate response until the system cooled the fluid.
The processor thermistor/sensor sends the signal that it needs more cooling. The peltier turns on and provides an immediate response until such time that a sensor in the fluid line registered that the fluid was cool enough to do the rest of the job. At that time the peltier would turn off.
The peltier and fluid temps could be programmable as to when they turned on/off. That way you don't have the peltier cooling "too much" before it turns off and, vice versa, the fluid getting "too cold" before the cooling pumps should turn off.
I sitll would like to see if a cube of Space Shuttle tile (Silica/Ceramic) would be a good heatsink. Problem is...the cost of prodution is so high. $1000 to $4000 for a single tile. Unknown how big a tile is at that price range and how many heatsinks it would make. But if a $1000 piece of tile could be cut into 10 heatsink cubes..that's $100 USD a piece.
Imagine...a heatsink that looks like a sugar cube strapped to the socket. No cooling fan required.
Now where's Thrax to shoot my theory down?
I didn't work directly on the shuttle, but I have been in the VAB several times and have handled pieces of tiles.
I would think that using a silicone based rubber cement would work best. We used to use something we called "Red Death" on the missile launchers to protect cable points, Blast surfaces and such. It would protect the metals from melting when hit by the missile exhaust during launches. We called it "Red Death" because if anybody opened a can of it anywhere in the building, everybody would have some on their clothes by the end of the day. Any stain from this stuff was forever. It mixed like a 2 part epoxy, applied like rubber cement, and set to a dense rubber consistency. It would hug the surface and not conduct heat either.
If there's anyone who would know about thermal heat shields it would be you Missleman. You're right about the the tiles. I got caught up in that demo of handling a tile while its core was still red hot. Got my physics backwards when it came to using it as a heat dissapating device.
I keep coming back to the problem of condensation. If you have something cold in a warm enviroment eventually there's going to be condensation. Without insulating the surrounding areas in a gunky mess of silicon or other such similar material...there is going to be the potential for problems. (By "cold" I mean near to the point of freezing.)
Hmmm....
Help me out here. Am I right in thinking that fluid that has a lower boiling point would be more efficient at carrying away heat providing that fluid eventually had some place to dissipate the heat to?
EG: A mercury filled system.
Or should I go back to school and take a few refresher chem and physics classes?
Still ...the concepts are layed out in John's original post and it could either fly or take an alternate route ...but it is workable.
Interesting concept John_D and thanks for the explanation MM!!
People in Arizona would have a lot less condensation trouble than us in Florida. The high amount of moisture in the air makes condensation on almost anything even cool. Our humidity is near 100% all the time and that's with a temp in the 90's.
When I was living at White Sands it was considered humid at 18% humidty. Never saw a drop of condensation while there. Even on the car air conditioners.
It might be an easier approach to the problem by removing the airs moisture.
We used to keep moisture out of Radar domes and the like to prevent arcing by filling them with a dry inert gas like nitrogen.
Dry air would work good enough in this instance. Maybe a de-humidifier on the air intake.
Just a thought for your perusal.
The question stands. Is there a fluid readiliy available and affordable (and also not a bio-hazard) that has a lower boiling point than water? Fluid additives such as Red Line Oil's Water Wetter are debatable as to their effectiveness.
Glycol?
(like this discussion has NEVER taken place before.
Just thinking
spark BOOM[
Or we'd have a buncha drunk Short-Medians because they finally figured out they could use their watercooling setup as a still.
I'm trying to think of various fluids that cool rapidly, toxic fluids have been included too:
Ethanol (Toxic)
Amonia (Toxic)
R12 Refrigerant (Non-toxic, non-flammable, non-corrosive)
R11 Refrigerant (Non-toxic, non-flammable, non-corrosive)
R22 Refrigerant (This one is specifically designed for compact cooling units) (Non-toxic, non-flammable, non-corrosive)
And any non-toxic synthetic HCFC might be applicable.
But really, closed-loop Ethanol is no more dangerous than running a skyy vodka cooling bong, or a micro-droplet vodka evaporative unit.
Use your computer for as an "alternate fuel" source producer.
We could market it like folding@home. Use the excess heat produced by folding/SETI to ease the local fuel/alcohol shortage.
We could make up and sell kits. We will be bigger than M$.
Who's in?
MM do you look good in Bill Gates glasses?
Pretty good for keeping fluid viscous at a colder temperature but think of the frost.
How do I respond to that? lol.
You're the rocket scientist here. Don't you have a gizmo kicking around that you put into a rocket to cool the circuitry? I know you probably do...knowing you'd want it quiet too so it doesn't drown out the rocket motors.
/me applies for government grant program for a research fund.
I had to research HCFCs and anti-coagulants for my submersion project.
I had to find something that wouldn't kill me.
Okay. lowest cost per unit of cooling is a stamped heatsink. The typical chunk o metal. The highest is watercooling and/or heatpipe based.
Any chilled watercooling setup runs the risk of condensation dependant upon the temperature. The cheapest form of a waterblock is naked machined metal.
What about reducing the overall size of the metal waterblock and encasing it within a good insulator of at least 1 cm thick? The only exposed metal would be what was in contact with the processor core.
There's something very cool working to the surface in this thread. hmm.
But who wants the mess?
So what's the thinest material that insulates against the cold extremely well? Neoprene "could" be a possibility. Better suited for the hoses.
What's a plastic material that, say, the waterblock could be dipped into to form a thicker barrier? The amount of grease could then be kept to near thermal paste amounts.
/me starting to cook in his room due to 2 other PCs churning away on benchmarks.
Okay...we get a waterblock...that technology has been taken care of. Anyone here work with insulating materials. Specfically vats o' insulating type stuff?
/me marvels at his own stunning grasp of technical jargon.
//EDIT:
Silicate, maybe? That's an anti-condensate...
I"m not saying plastic...but what material can be shaped around a waterblock or cut to have the waterblock fit inside? The waterblock would simply have to be custom made to have a sugar cube sized protusion on the bottom. That would be what would come in contact with the processor core. The insulating material would be flush with that.
Thrax?
wool?
EDIT/
Silicate. Now we are back to the space shuttle tile talk. Plus its known to produce sandy debris like sanding a piece of wood. And HIGHLY expensive. But we are onto something.
EDIT EDIT/
Think Man...think! Insulating material that is thin and can be machined. Two halves: top and bottom. Bottom has a square hole to receive the CPU contact plate which is also machined onto the metal waterblock as a "bump". Top has hole(s) to allow for the hoses. The two are screwed together with a silicon rubber seal between. No mess. Small tube of dielectric grease supplied in kit.
IDEA copyright Thrax and MM 2004.
Proper condensation requires more evaporation/condenstation space than a tiny channel. The "waterdom" idea has more legs. Err..."blocksleeve"?
The red part is where water would condense and drain off.
Draw yours for me, MM.
The waterblock would be machined with a protusion. That protusion would then be flush with the bottom of the insulating package which would come in a top half and bottom half. The seal between the two would be a rubber/silicon gasket and the cross section is shown thusly.