I'm working on developing an affordable metal 3D printer. This printer would be a RepRap style printer, using a MiG welder to deposit material. In theory, I should be able to have 0.023" beads (0.6 mm). It would be coarse compared to current FDM printers, but with other welding technologies (lasers!) this would be able to go much smaller. This printer would require a starter plate for each weld. And the target market cost would be $3500.
I have most of the physical parts in place, and I'm starting to work on building controls for it, which is where I've hit a snag.
I have a basic level of programming knowledge, and I can write basic codes in C / C++ and understand the gist of what others have done. But the changes I need (understand the current firmware, change as required for my printer) are beyond my immediate skill level. I plan on learning more Arduino and looking through the Marlin firmware the chassis I built is designed to work with, which is a Kittaz without the heating bed and plastic extruder.
The changes I need are in two phases:
1) Simple, demonstrate concept change
a) Change from stepper motor controlled extrusion to Power on / Off
b) Eliminate temperature controls and stops (no heated bed, no heated extruder
With this phase, I plan on using Slic3r with constant feed rates and speeds, and manually tuning the wire feed, voltage, and amps on the welder to get a working print.
2) Long term production phase
a) Interface with welder to control wire feed
b) Interface with welder to control voltage / amps
In this phase, I hope to either build / source a stand alone power source and control for the welding, or work with the supplier to integrate controls.
I'm currently working with this firmware.
With that said, I would rather get this thing out and available sooner rather than later. And waiting an unknown number of weeks while I learn this code seems like a long time, when there are people asking for this technology every day. Would anyone be interested in taking a look into helping me with this task? I'm looking to team up with someone with this knowledge and working together to tune the system and bring this to market via Kickstarter and/or RedditMade.
Hired a Mech. Eng. Dev from ODesk - guy seems like he knows whats up, and wasn't charging me crazy amounts.
His proposed solution was simple: take the output from the 3D printer that would normally send a pulsed output to the stepper motor, and convert that to a on/off signal to a solenoid via another smaller, controller. He would program that board, and I need to figure out how to mount a solenoid.
No big deal, and suddenly I'm back on track to getting this thing running by the end of the year!
Thanks all for the advice via PM and otherwise about ODesk Really seems to work well. Its also worth noting you can list yourself as a 3D modeler / designer on that site, which I will be taking advantage of.
@d3k0y said:
I know a guy that does actual welding, if you need assistance on making the arcs any better, he might be able to help.
What I need is an affordable weld end (MIG, TIG or otherwise) that can do a smaller weld. I'm assuming I'll have to go with lasers. If your guy knows any solutions of that sort, that'd be awesome.
Most of the problem I had is that the mig welder I am currently using isn't meant for "small" welds. I'm using 0.023" wire, and no combination of the settings I found was able to do a small AND constant weld. I can do one or the other, not both.
I want an individual throttle body manifold for my 6M-GE Toyota engine inline six that will mount 4A-GE ITBs but maintain my existing fuel rail and injectors. Basically, I want this but for my six cylinder:
Can you 3D print a manifold that can handle engine temps and exposure to fuel?
I have two sets of 4A-GE ITBs that need a home under my hood
Because racecar.
came here for the engineering, left with a car hard on...did this ever happen??
just mirror the square part to be on both sides...tighten and loosen. same idea as ratcheting box end wrenches. no selector, just flip the wrench over.
@XGPHero said:
just mirror the square part to be on both sides...tighten and loosen. same idea as ratcheting box end wrenches. no selector, just flip the wrench over.
I can make that. The smallest step I've been able to do well with is .2mm, which looks not quite add nice as this, but better than I've posted here in a while. I'll take some pictures of something with better experience behind it.
Comments
Bencon cusom eng...
http://www.sciencealert.com.au/news/20142706-25757.html
I want to do a project like this:
https://www.kickstarter.com/projects/460400892/affordable-3d-metal-printer-aurora-labs
https://www.gotorch.com/order-low-cost-cnc.html
Questionmark?
If I had an extra $3k around, I would get this or something like it. I will definitely be in the market soon.
Ryanfodder, you should get in on this:
https://redditmade.com/about-us
Small scale opportunity, but could be incremental while letting you build a portfolio of products.
I saw that this morning. Not sure what I would do. I think it would be pretty cool though.
Seems like a mini-kickstarter.
I'm working on developing an affordable metal 3D printer. This printer would be a RepRap style printer, using a MiG welder to deposit material. In theory, I should be able to have 0.023" beads (0.6 mm). It would be coarse compared to current FDM printers, but with other welding technologies (lasers!) this would be able to go much smaller. This printer would require a starter plate for each weld. And the target market cost would be $3500.
I have most of the physical parts in place, and I'm starting to work on building controls for it, which is where I've hit a snag.
I have a basic level of programming knowledge, and I can write basic codes in C / C++ and understand the gist of what others have done. But the changes I need (understand the current firmware, change as required for my printer) are beyond my immediate skill level. I plan on learning more Arduino and looking through the Marlin firmware the chassis I built is designed to work with, which is a Kittaz without the heating bed and plastic extruder.
The changes I need are in two phases:
1) Simple, demonstrate concept change
a) Change from stepper motor controlled extrusion to Power on / Off
b) Eliminate temperature controls and stops (no heated bed, no heated extruder
With this phase, I plan on using Slic3r with constant feed rates and speeds, and manually tuning the wire feed, voltage, and amps on the welder to get a working print.
2) Long term production phase
a) Interface with welder to control wire feed
b) Interface with welder to control voltage / amps
In this phase, I hope to either build / source a stand alone power source and control for the welding, or work with the supplier to integrate controls.
I'm currently working with this firmware.
With that said, I would rather get this thing out and available sooner rather than later. And waiting an unknown number of weeks while I learn this code seems like a long time, when there are people asking for this technology every day. Would anyone be interested in taking a look into helping me with this task? I'm looking to team up with someone with this knowledge and working together to tune the system and bring this to market via Kickstarter and/or RedditMade.
Hired a Mech. Eng. Dev from ODesk - guy seems like he knows whats up, and wasn't charging me crazy amounts.
His proposed solution was simple: take the output from the 3D printer that would normally send a pulsed output to the stepper motor, and convert that to a on/off signal to a solenoid via another smaller, controller. He would program that board, and I need to figure out how to mount a solenoid.
No big deal, and suddenly I'm back on track to getting this thing running by the end of the year!
Thanks all for the advice via PM and otherwise about ODesk
Really seems to work well. Its also worth noting you can list yourself as a 3D modeler / designer on that site, which I will be taking advantage of.
So, I have a basic metal printer that can do very non-detailed stuff. Any ideas what I should do as a demo?
Here's the first bits of playing around, trying to get the arc right:

And I got the arc going a lot better here, decided to make something more memorable.
And my final calibration peice. The part is much thicker than I'd hoped, but I can make stuff with it still!
Yay!
I know a guy that does actual welding, if you need assistance on making the arcs any better, he might be able to help.
What I need is an affordable weld end (MIG, TIG or otherwise) that can do a smaller weld. I'm assuming I'll have to go with lasers. If your guy knows any solutions of that sort, that'd be awesome.
Most of the problem I had is that the mig welder I am currently using isn't meant for "small" welds. I'm using 0.023" wire, and no combination of the settings I found was able to do a small AND constant weld. I can do one or the other, not both.
came here for the engineering, left with a car hard on...did this ever happen??
From my buddy
"i'd have to see it in action
from what i saw it kinda looked like he was moving way to fast"
I'm going to try very slow when I get it running again and see what happens.
Thanks!
That's what she said.
1/4-in drive anyone?
http://nasa3d.arc.nasa.gov/detail/wrench-mis
Do you know what material they used? 3 in-lbs isn't a lot of torque, but any plastic part printed will easily sheer between layers.
Nailed it!
Most appropriate use for 3D printing I've seen yet.
just mirror the square part to be on both sides...tighten and loosen. same idea as ratcheting box end wrenches. no selector, just flip the wrench over.
That makes too much sense!
ABS.
Can you make something like this?
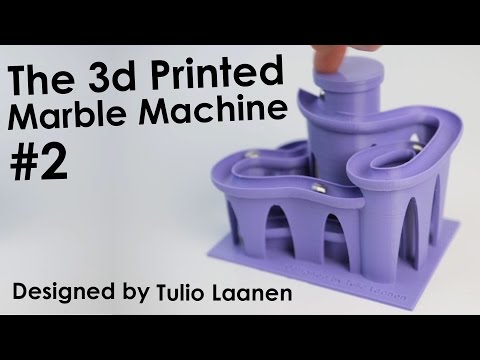
The 3d print looks a bit smoother than your setup?
http://www.thingiverse.com/thing:795952
I can make that. The smallest step I've been able to do well with is .2mm, which looks not quite add nice as this, but better than I've posted here in a while. I'll take some pictures of something with better experience behind it.
Here are a couple of my most recent prints.
That knob design fixed both the stove and the dryer at ICHQ.
Linc loves well-shaped knobs he can grip.